SVG – Static VAR Generator

Maintenance Free
The SVG operates without mechanical components, thereby avoiding maintenance and replacement of components.

Save Money and Secure Compliance
Optimize the performance of your electrical installation and eliminate the utility company’s monthly surcharge for both inductive and capacitive energy.

Increased Safety
By removing the weakest link the SVG eliminates electrical safety risks and component failure risks associated with capacitor baced systems. No risk of resonance, fire or explosions.
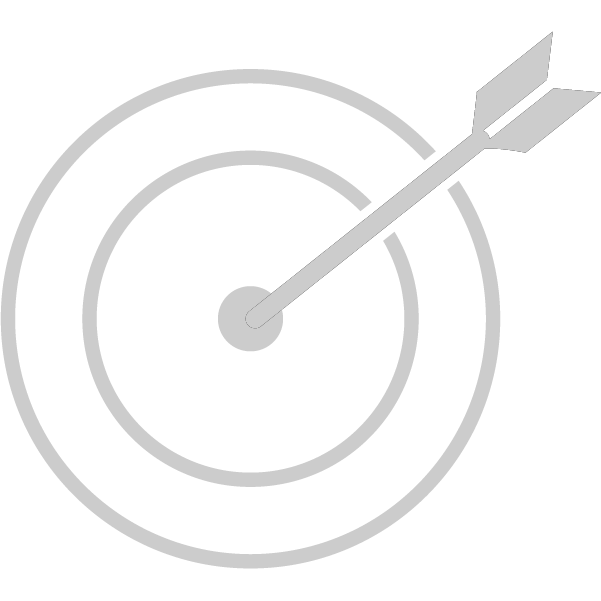
Maximum Accuracy
The unit dynamically compensates the exact amount of reactive current to achieve the set target value.

Stepless – Transient Free Compensation
Unlike conventional compensation units using contactors, no transients occur as the technology is not based on the connection of capacitors.

A REVOLUTIONARY NEW POWER FACTOR SYSTEM – STATIC VAR GENERATOR (SVG)
EMES SVG is an entirely new approach to power factor correction, current balancing, voltage balancing, voltage regulation and VAR support. Ideal for industrial, commercial and electricity network applications.
The SVG utilises a high speed three level inverter that reacts to changes in reactive power, exchanging corrective reactive power into the system. Full correction is made in 3/4 of a cycle. This rapid response provides stable accurate real-time power factor correction without the drawbacks of traditional capacitor based systems.
Key functions:
- Dynamic step-less power factor correction
- Active Load balancing
- Voltage variations (sags&swells) reduction.
- Voltage fluctuations (flicker) mitigation
How EMES SVG works
The new EMES SVG has the same operating principle as the APF and is basically a very advanced computer controlled current generator, with the ability to instantly produce any shape or form of compensation current.
Dynamic Power Factor Compensation
The EMES SVG series represents the latest generation technology in the power factor correction field. It operates by detecting the load current on a real-time basis through an external CT’s and determining the reactive content of the load current. The data is analysed and the SVG’s controller drives the internal IGBT’s by using pulse width modulation signals to make the inverter produce the exact reverse reactive current of the corresponding load reactive content. This is injected to the grid to compensate the reactive content of the load current. By adjusting the output voltage amplitude and phase angle or by directly controlling the AC side current, the SVG can absorb or generate var according to the load reactive power or the grid voltage level.
Real time dynamic compensation
Traditional capacitor type PFC systems take 20ms-40s to respond to a change in load. Their delay combined
with the stepped response performance means that they are perpetually over or under compensating
Load Balancing
Using single-phase loads on a three-phase electric power system (connected phase-to-phase or phase-to-neutral) results in unbalanced load conditions in the system. Unbalanced load currents result in unbalanced voltages and affect other loads connected at the point of common coupling. Unbalanced load conditions also cause excessive neutral current, resulting in overheating motors and transformers, power losses and lower system efficiencies. Load balancing is necessary to improve the power quality and efficiency of the system. A typical case where load balancing is needed is a phase-to-phase connected welding equipment and AC – EV chargers that burdens only two of the three lines and can thus create voltage unbalance between the phases
Revolutionary new PFC System - Eliminating the weakest link
Dynamic step-less compensation
The SVG provides real time response with constant correction to plant power factor. Transient free, virtually instantaneous response ensures high system stability.
SVG provides a continuous correction – step less control. SVG controls from 0 – rated kVAr as one continuous range.
The SVG is unaffected by network voltage drop. Even under reduced network voltage levels full reactive current can be provided to meet working conditions. Operating voltage range of -40% to +20%
Profiles the load and operates with a response speed of <15ms
Dynamic reaction time is less than 50μs
No possibility of over-compensation or under-compensation as experienced capacitor switching systems
Only injects the kVAr that is needed in that moment
Individual correction on all three phases.
Over and under compensating
Traditional capacitor type PFC systems are slow to react to load changes. Their delay combined with stepped response means
they are perpetually in a state of under compensation or over-compensation
Ultra fast dynamic compensation
The Static VAR Generator recalculates the required load accurately and quickly.
The IGBT technology switches with ultra high speed, quickly matching the load requirement.
SVG Reaction Time <50µs, response time < 15ms
50µs response time with full correction in less than 15ms (3/4 of a cycle).
Suitable for highly dynamic loads where the power factor fluctuates rapidly or in big steps e.g. saw mills, cranes, welders.
Technology
Designed for high performance and reliability
We can proudly say that our products are designed and manufactured to the highest specifications using the proven IGBT (insulated-gate bipolar transistor) power switching semiconductors and digital signal processing hardware to secure high performance and accurate control.
By using state-of-the-art signal processing and advanced control structures to manage the power flow to and from the machine, EMES SVG technology continuously monitors the network and injects the exact right amount of compensation current, at exactly the right time.
EMES Static VAR Generators are built on modern three-level topology, which brings several major benefits compared to other active filters built on the conventional two-level topology. With three-level topology technology, the switching frequency and voltage stress are distributed among the two IGBTs. Reduced stress extends the lifetime of the power electronics. The efficiency and lower losses achieved with three-level topology are substantial. These improvements reduce the overall cost of ownership compared to conventional solutions.
The advanced 3 level topology design based on a zero level voltage transformation (comprising of IGBT’s of lower voltage corresponding higher switching frequency).
EMES SVG`s are capable of suppressing the undesirably generated ripple currents effectively and promote a high compensation precision for the output waveform with respect to the sinusoidal waveform.
Key Features
- Real time, dynamic step-less compensation
- The new EMES SVG Profiles the load and operates with a dynamic reaction time is less than 50μs and a response speed of <15ms. The SVG has the capability to deliver instantaneous capacitive and inductive reactive power compensation with no possibility of over-compensation or under-compensation. The SVG is optimized for highly dynamic applications where conventional capacitor banks or reactor banks are unable to track the loads.
- Unlimited scalability and flexible design.
- Higher compensation capacity can easily be achieved by adding SVG modules in parallel without any technical limitations. This give the flexibility to facility engineers when more loads are added in the facilities.
- Market leading technology – 98.5% best in class efficiency
- With unbeatable technology and cutting edge capabilities, the new EMES APF range drastically lowers your installations and operational cost. Energy losses are reduced by 50%, and 33% heat reduction ensure improved equipment and cost efficiency.
- Long life with extreme durability – maintenance free .
- SVG uses power electronics to correct the power
factor. As there are no passive elements, the device
can be installed in any type of network with a high
harmonic current presence without affecting its
performance. The SVG operates without mechanical
components, thereby avoiding maintenance and
replacement of components.
- SVG uses power electronics to correct the power
- Balance your load and correct your power factor.
- One device, but many solutions to help you save energy, achieve higher productivity, decrease downtime and extend lifetime of devices and components.
- Real time access, monitoring and configuration
- Advanced and comprehensive monitoring & reporting features. They enable before and after analysis by providing you data of harmonic distortions from both supply and load side. The Easy to use high quality colour display allows the device to be configured and its installation status shown in real time.
SVG vs Capacitor Bank
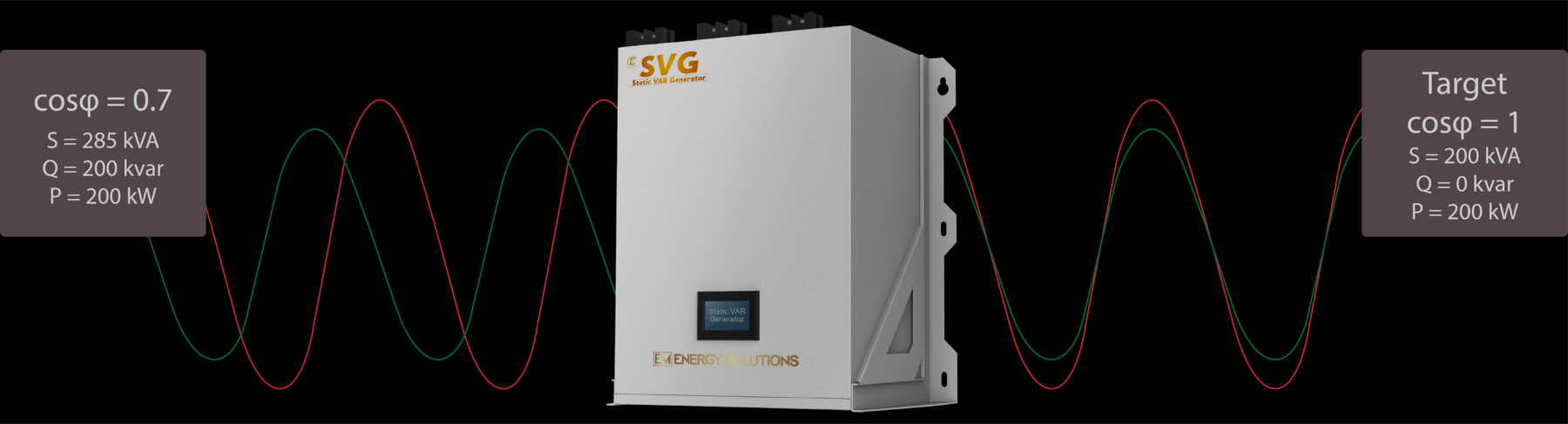
Modular, compact size and light weight
Due to the operational temperature and safety requirements applicable to capacitor banks, traditional PFC systems are constructed as a separate, stand-alone assembly or in self-contained spaces within the overall construction of the main switch board.
This results in the common situation where PFC systems occupy a large space, often taking up valuable floor space in switch rooms.
EMES have applied new generation thinking and innovative design principles to create a new generation of PFC solutions that has redefined what is possible from a cost vs performance vs space perspective.
EMES SVG are a modular design that are available in wall-mount, rack-mount and rack/cabinet configurations.
This flexibility gives engineers multiple options to cater for all situations and ultimately save valuable space and floor real-estate.

Rack mounted module
The new EMES Static VAR Generators are designed for light industrial, commercial buildings and demanding applications with voltage level up to 690V in both 3W and 4W applications.
Ultra-compact design makes it suitable for space limited application, retrofit projects and allows easy integration into variable speed drives (VFDs) or capacitor bank cubicles.
Rack mounted modules are available in single module capacity from 30KVAR – 250KVAR, with unlimited parallel installation capability.
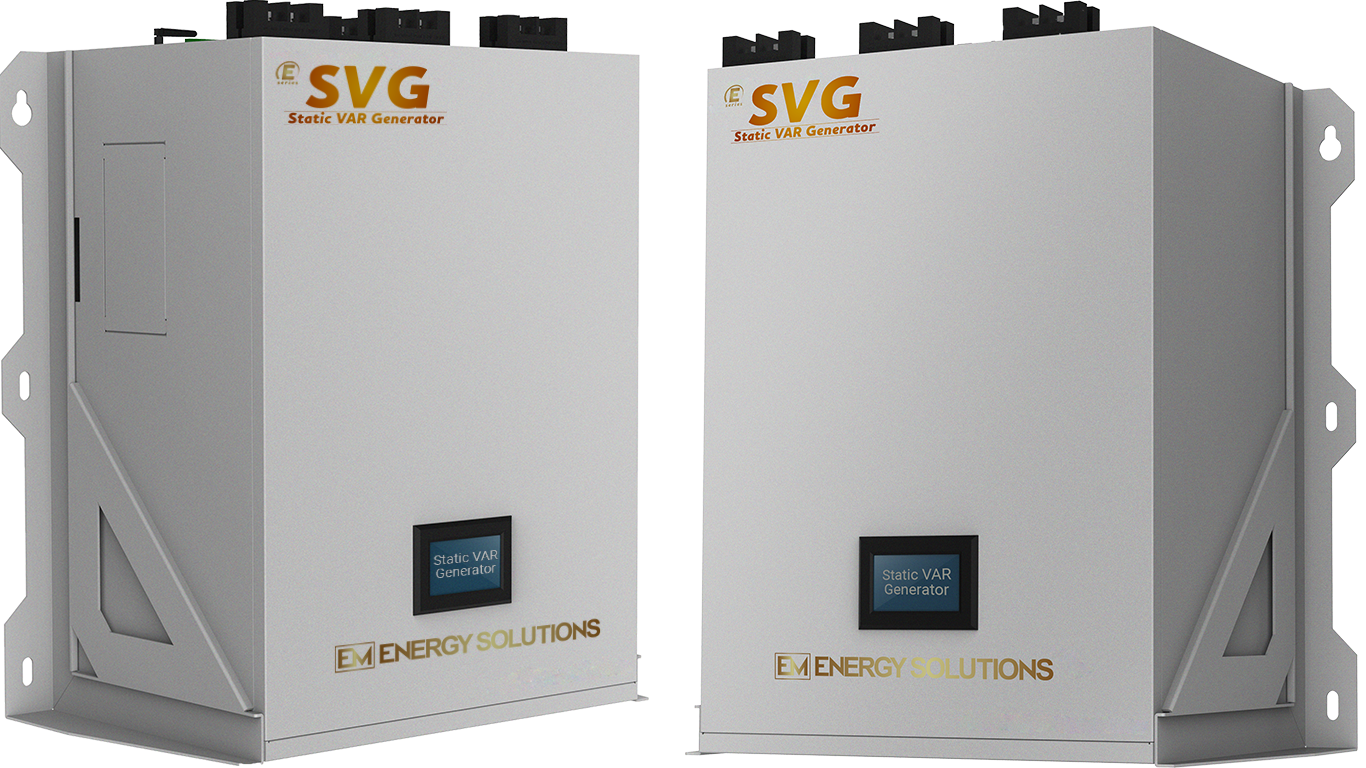
Wall mounted module
The wall-mounted E and H series SVG`S are a complete space effective solution for dynamic step less PFC in three-phase industrial, commercial or service installations.
Wall mounted modules are available in single module capacity from 30KVAR – 250KVAR, with unlimited parallel installation capability.

Flexible cabinet solutions
EMES offers a wide range of flexible and modular cabinet options. Cabinets are avilable in IP20, IP31, IP54 or others degrees of protection upon request. Cabinets are easelly expandable with small-sized rack modules and up to 900A maximum capacity in one cabinet.
The cabinets are pre-installed, pre-wired, pre-configured and tested for quality before shipment.
The flexible functionality of the cabinets allows integration to overlying control such as a PLC or SCADA systems.
Applications
The SVG’s unique features makes it a multi -purpose unit for low and medium voltage up to 38.5 kV. The SVG can be installed for multiple applications, whether in the industrial or the services and infrastructures sector. Industrial furnaces, welding equipment, electric motors with variable speed drives, telecommunications infrastructures, hospitals or airports (lifts and escalators), water industry, data centers, paper industry, electric generators are examples of typical applications.
Many industrial facilities place poor power quality at the top of the list of inefficiency factors responsible for losses due to reduced productivity and lower quality of products. Optimal electrical power utilization becomes a challenge, as well as a necessity to keep up with ever increasing energy demand without drastic increases in energy costs.
Large industrial, commercial and institutional power users can benefit from centralized medium voltage SVG reactive power compensation systems.
Advanced Performance – HIGH STABILITY AND NETWORK FRIENDLY
The new method of PFC from EMES takes away the most vulnerable and weakest link in a traditional PFC system – the switched capacitors. Various environmental conditions (eg. excessive temperature, over-voltage, harmonic distortion) may cause capacitors to rupture and ignite. Unlike traditional capacitor based systems, the SVG does not negatively interact with your electrical system. Today’s harmonically rich environments are tough on capacitor based systems with increased risks of resonance and capacitor failures:
• Unaffected by harmonic distortion and free from harmonic resonance
• Three phase unbalance compensation
• Unaffected by network voltage drop. Even under reduced network voltage levels full reactive current can be provided to meet working conditions. Operating voltage range of -40% to +20%
• There is no nasty transient voltage spikes caused by the switching of capacitors
• Overheating capacitors and harmonic reactors are a thing of the past.
• Allow compensation of loads fed by generators without risk of overcompensation.
• <3% THDi input harmonics won’t pollute the network
• Inject reactive power that is required by the load at each instant into the system.
• Capacitor free. Gone are the days of constantly checking capacitors for degradation or failure
• Low risk – no swollen or leaking capacitors. Reduced fire risk
The SVG has a design service life of more than 100,000hrs, without maintenance.
That’s more than 10 years operation in a plant that operates 24/7. in comparison capacitor based systems can last as little as three years.
Power Factor
Power factor is an expression of energy efficiency. It is usually expressed as a percentage—and the lower the percentage, the less efficient power usage is.
Power factor (PF) is the ratio of working power, measured in kilowatts (kW), to apparent power, measured in kilovolt amperes (kVA). Apparent power, also known as demand, is the measure of the amount of power used to run machinery and equipment during a certain period. It is found by multiplying (kVA = V x A). The result is expressed as kVA units.
PF expresses the ratio of true power used in a circuit to the apparent power delivered to the circuit. A 96% power factor demonstrates more efficiency than a 75% power factor. PF below 95% is considered inefficient in many regions.
Poor power factor means that you’re using power inefficiently. This matters to companies because it can result in:
- Heat damage to insulation and other circuit components
- Reduction in the amount of available useful power
- A required increase in conductor and equipment sizes
Low power factor increases the overall cost of a power distribution system because the lower power factor requires a higher current to supply the loads.
What is Power Factor?
Power factor basics
Power Factor is a measure of how effectively incoming power is used in your electrical system and is defined as the ratio of Real (working) power to Apparent (total) power.
Real Power (KW) is the power that actually powers the equipment and performs useful, productive
work. It is also called Actual Power, Active Power or Working Power.
Reactive Power (KVAR) is the power required by some equipment (eg. transformers, motors and
relays) to produce a magnetic field to enable real work to be done. It’s necessary to operate certain
equipment but you don’t see any result for its use.
Apparent Power (KVA) is the vector sum of Real Power (KW) and Reactive Power (KVAR) and is the
total power supplied through the power mains that is required to produce the relevant amount of
real power for the load
Power Triangle
The relations between the various power components are illustrated in the power triangle shown above.
From the figure, it is apparent that the active power component is in phase with the applied voltage
while the reactive component occurs 90º out of phase with the voltage.
The equation that defines this relationship is:
(kW)2 + (kVAR)2= (kVA2)
Reactive power creates an additional load on the cables, wires, and electrical equipment itself. Too much reactive power can cause overheating of the components which significantly shortens the lifetime of equipment. In addition, it can contribute to unintended shutdowns, power losses, blackouts, and even fines for not complying with power quality standards and regulations.
All in all, reactive power negatively affects electric efficiency and causes unnecessary energy losses, shorter lifetime of components and higher energy consumption and other extra costs.
Let’s look at a simple analogy in order to better understand these terms. Let’s say you’ve ordered a glass of your favorite
beer. The thirst quenching portion of your beer is represented by Real Power (KW).
Unfortunately, along with your ale comes a little bit of foam that doesn’t quench your thirst, represented by Reactive Power
(KVAR). The total contents of your glass (KVA) is this summation of KW (the beer)
and KVAR (the foam).
The power factor is the ratio between Real Power and Apparent Power. It’s expressed as a value between -1 and 1 and can be either
inductive (lagging) or capacitive (leading). If the power factor is 1, then all of the power supplied is being used for productive work
and this is called ‘unity’.
Therefore, for a given power supply (KVA):
The more foam you have (the higher the percentage of KVAR), the lower your ratio of KW (beer) to
KVA (beer plus foam). Thus, the poorer your power factor.
The less foam you have (the lower the percentage of KVAR), the higher your ratio of KW (beer) to
KVA (beer plus foam) and the better your power factor. As your foam (or KVAR) approaches zero,
your power factor approaches 1.0 (unity).
A power factor of -0.7 for example, indicates that only 70% of power supplied to your business is being used effectively and 30% is being wasted. The wasted power is the Reactive power (the foam in the previous example). Most loads are inductive in nature, which means the power factor will typically be less than unity. The further the power factor is from unity, the greater the apparent power drawn and therefore, the greater the current draw for the system.
The increased current may require an increase in the size of your transformers and installation power wiring. Increased current also results in increased heat which affects the longevity and lifespan of an electrical system. This can add a great deal of cost to the installation and may also limit the expansion of a plant.
Get a free consultation today
Contact us today for advice about your unique operation
Why is Power Factor important?
It’s important because you may be paying for reactive power (foam) that you cannot use to power equipment. If you can reduce the foam, you can get more ‘beer for your buck’.
Improving the power factor results in less current being drawn, therefore less electricity costs, less heat and greater longevity of the electrical system.
Many power suppliers charge for the base load (kW) and a maximum demand tariff. If this maximum demand tariff is measured in kVA, then improving the power factor reduces the kVA of the installation, thus reduces the maximum demand tariff and thereby reducing your power costs.
It is actually a network regulation that customers maintain a specific minimum power factor (values
depend on your region). Utility companies may charge customers a penalty on top of consumption charges when customer power factor is less than a determined value.
Get a free consultation today
Contact us today for advice about your unique operation
What is Power Factor Correction? How can it help your bussiness
Poor Power Factor can be improved by installing Power Factor Correction (PFC) equipment. Traditional solutions incorporate banks of capacitors that work as silent reactive power ‘generators’, often housed in a metal cabinet similar to the one that houses your electrical switchboard. EMES offers the latest generation of advanced performance PFC solutions that do not need a capacitor bank and offer many advantages due to their compact and modular configuration.
How Can Power Factor Correction Help You?
An electrical load with a poor power factor draws more current than a load with an improved power factor for the same amount of useful power transferred and can put unnecessary strain on the electricity distribution network. By improving your power factor, you can reduce your electricity bills through lower monthly demand and capacity charges. Typically payback periods for power
factor correction are between 1-3 years. Given the life expectancy of power factor correction equipment and the potential savings, it can be a very worthwhile investment.
Poor power factor may cause power losses and voltage drops, which can contribute to overheating and failure of motors and other equipment. If your electrical system is near capacity, installation of power factor correction equipment may help avoid costly infrastructure upgrades by lowering the existing electrical demand on your system and improving efficiency stability
THE BENEFITS OF ADDRESSING POWER FACTOR
• Lower operating costs by using power efficiently, lowering distribution
costs, and avoiding electrical network penalties
• Low power factor can cause overloading of cables, switchboards, transformers,
and other electrical infrastructure
• Reduces the threat of operational downtime caused by overloading of
electrical assets.
• Low power factor can cause reduced levels of site voltage and consequently
present unreliable equipment performance.
Get a free consultation today
Contact us today for advice about your unique operation
Harmonics Distortion - True Power Factor
True Power Factor – Displacement or Distortion?
There are two components of PF and it is crucial to understand them both to choose the right solution to improve it. Otherwise, you could be making things worse!
Traditionally, PF is less than 1 because of inductive loads such as motors, which are considered linear devices. A linear device is defined as a device for which the output is, within a given dynamic range, linearly proportional to the input.
These loads need reactive power to create a magnetic field to do real work. This reactive power leads to a phase shift between the current and voltage waveforms. This results in a decrease in average power and gives rise to Displacement Power factor.
Today, with the heavy proliferation of nonlinear loads, low power factor on a power system is often
the result of high distortion reactive power components and not inductive reactive power. Therefore, in this case, one can no longer say that low power factor is normally caused by electric motors and other inductive loads. And, since the best and safest way to improve a poor power factor caused by non-linear loads is to remove the harmonic currents, the traditional means of adding power factor correction traditional capacitors is, quite often, no longer suitable.
Non-linear devices draw current that does not have the same waveform as the supply voltage, the relationship between current and voltage is not linear.
Non-linear devices are sources of harmonics, and this leads to current and voltage distortion, giving rise to another component of Power Factor, which is known as Distortion Factor.
The presence of current and voltage harmonics increases business operating costs by increasing downtime, placing undue burden on the electrical infrastructure, and making PF correction difficult.
True/Total PF = Displacement PF * Distortion Factor
Trying to correct Distortion Factor with a capacitor bank could exacerbate the situation and cause even more damage due to a phenomenon known as resonance.
The Problem with traditional capacitors and harmonic distortion
When applying power factor correction capacitors in the presence of harmonics, a couple of issues come to surface.
First, capacitors are a natural low impedance path for harmonic currents and will, therefore, absorb these energies. This increase in capacitor current results in higher element temperature which reduces the life of the capacitor. Also, because capacitors reduce the network impedance, capacitors can actually increase the level of harmonic current on the network.
It is important to remember that while capacitors do not produce harmonic currents, they can magnify their
effects. Furthermore, harmonic voltages present on the network create voltage stresses on the capacitor.
The second and potentially more serious concern, is network resonance. When capacitors are added to the network, they set up a parallel resonance circuit between the capacitors and the network inductance. Harmonic current components that are close to the parallel resonance point are magnified. The magnified current can cause serious problems such as excessive voltage distortion, nuisance fuse and breaker operation, over voltage tripping of drives and insulation breakdown within motors, transformers and conductors. Both risks increase with the size of the capacitor bank. The larger the size of the capbank, the higher the risks
Knowing your true PF is crucial for implementing the right solution
Contact us today for advice about your unique operation
The evolution of power factor correction

COMPREHENSIVE MONITORING AND REPORTING features
Easy to Use Graphical User Interface
EMES SVG come with advanced and comprehensive monitoring & reporting features. The Easy to use high quality colour display allows the device to be configured and its installation status shown in real time.
In the SVG monitoring system you can instantly view:
- The power quality levels of your system
- Your system status
- The overall performance of the system
- Power quality data
- Phase order
- Power levels
- Harmonic spectrum
- Waveforms
- System configuration
- Compensation configuration
- Alarm and event history
- Trigger events and warnings
Quick installation and easy step start-up.
The device just needs to be connected to the filter’s network and measurement transformers, configured using its touch screen and then started up. The device itself will check that start-up is safely carried out thanks to an internal self-diagnosis system.
Easy device configuration with clear, guided steps.
Easy operation mode selection
Rack and wall mounted modules
Can be equipped with 4,3″ high quality touch screen Easy to use, with displays on every unit
providing all system information including grid voltage, compensating current, grid current, load current, grid PF, load PF, alarm
code and operating status.
Cabinet based systems
Come complete with centralized 7” LED colour TFT touch screen. The HMI so you can see exactly what is happening with your complete system. In addition to the information available on the standard unit display you can view individual module temperatures, THDv, THDi, voltage waveforms, harmonic spectrum in real time.Information is displayed to the user in a very visual way by graphs and diagrams, so the behavior of the installation and device may be instantly checked . The device also displays information for the 5 seconds prior to alarm activation to totally control installation status.
Optional
Remote access and wireless access point with integrated web server and 4G modem. (WiFi-4G-WAN-LAN)
Real-time, online, website monitoring of instantaneous values.
Data download without requiring any software.
Ethernet: TCP/IP, Modbus TCP.
Remote configuration and support of the device.
medium voltage and Special applications
Medium voltage applications
EMES have extensive knowledge from MV applications and with utilizing our standard units and industry-proven low voltage Active Filter with a step up transformer to create medium voltage solutions. If applied correctly, an active technology is very compact and flexible enabling high availability. EMES multifunctional modular design offers a high degree of redundancy and availability as the modules can be operated individually.
Large industrial loads, such as arc furnaces, welding equipment, rolling mills, and large induction motors used in various industries, significantly affect the stability and operation of the power system by causing flicker, voltage unbalance, and harmonic distortion.
With the ultra-fast response time of less than one millisecond, EMES active units ensure superb compensation of reactive power and harmonic distortion even for rapid varying large loads. The compensation increases the plant’s productivity and removes damaging power quality challenges like flicker and harmonic distortion.
Application areas include:
• Steel industry (Electric Arc Furnaces – voltage stabilization reduces tap-to-tap time and electrode consumption.)
• Mining and heavy industry – dynamic reactive power compensation stabilizes the power system, especially on large motor start-up, ensuring a reliable power system.
• Shredders and crushers
• Welding (Shipyards)
• Cement plants
• Cranes
• Renewables markets like solar farms, wind farms, solar panel installations
• Regulating voltage and reactive power in transmission and distribution lines
Custom projects and Special Applications
EMES delivers customized solutions tailored by your needs.
Examples on such customization could be harsh environment adoptions like, high temperature, salt and humid environment and special IP or certification requirements.
We also have long experience with containerized solutions, and we can provide tailored systems with plug and play functionality with all necessary accessories and certifications.
AVE-Hybrid (AVE+SVG - Best of two worlds)
By combining the AVE and the new Staic VAr Generator the AVE-Hybrid is capable of controlling both
current and voltage, making it capable of addressing almost all known power quality related problems
we see today and guarantees an optimal protection and power quality in your plant. The SVG part of the hybrid solution ensures an accurate and effective removal of system harmonics, load balancing, and a dynamic real time power factor compensation.
The AVE part reacts with the speed of the current, mitigates fast switch transients and protects the installation against voltage surges. The unit also reduces voltage dips and its effects together with ensuring a clean and stable ground reference, which again will reduce the risk of control system lockups.
The AVE – Hybrid gives longer equipment lifetime, higher process reliability, improved power system capacity and stability, and reduced energy losses, complying with most demanding power quality standards and grid codes.
Technical Specifications
EMES new range of revolutionary power factor system is compatible with all three-phase low voltage applications. The multi-functional dynamic PFC solution brings reliability and efficiency to your electrical system, resulting in greater operational efficiency, prolonged equipment life and improved energy efficiency.
E-Series
E – Series – Static VAR Generator
E-series SVG gives you everything in a compact format. Although compact and cost-effective, the E-series features cutting-edge performance including excellent dynamic power factor compensation capability. E-seires is the ideal PFC solution for small and medium size commercial and industrial loads. It is a powerhouse solution and the best choice for most applications because it is such a general purpose PFC.
- Real-time dynamic VAR compensation
- Load balancing
- Voltage control
- Ultra fast and accurate response
- Idle mode during low load (Standby)
- Non-over loadable
- Anti resonance protection and self diagnostic system
- Comprehensive monitoring system with high quality HMI
- Compact, modular and scalable design
- Wall-mounted, rack mounted and flexible cabinet solutions
Item | Static Var Generator | |||
SVG 30 | SVG 50 | SVG 100 | SVG 200 | |
Electrical ratings – System parameters | ||||
Rated voltage | 400 V – (auto sensing). Connection to higher voltages through suitable step-up transformer | |||
Voltage Range | 228 ~ 456 Vac +/-10% | |||
Nominal Frequency | 50/60 Hz (auto sensing). | |||
Parallel modules | Unlimited scalability – Unlimited parallel capacity -Load shared evenly between modules | |||
Efficiency | ≥ 97 % | |||
Electrical system compatibility | 3-phase 3-wire and 3-phase 4-wire | |||
Current Transformer | 0 ~30,000/5 | |||
Topology | 3-level NPC inverter topology (IGBT). Switching frequency 20kHz | |||
Performance Indicators | ||||
Capacity | 30 kvar | 50 kvar | 100 kvar | 200 kvar |
Power factor correction | Optimized, stepless and continuously adjustable power factor correction, leading (capacitive) and lagging (inductive). | |||
Unbalance Comp. | 0-100% | |||
Reaction / response time | 50µs response time with full correction in less than 15ms (3/4 of a cycle) | |||
Target PF | -1 ~ 1 Adjustment | |||
Overall Resonse Time | FFT, Intelligent FFT and Instantaneous Reactive Power | |||
Switching Frequency | Average 20 kHz | |||
Cooling (Smart Ventilation) | 115 L/Sec | 222 L/Sec | 360 L/Sec | 500 L/Sec |
Noise Level | < 56 dB | < 56 dB | < 65 dB | < 75 dB |
Monitoring | ||||
Communication Port | RS485, Ethernet, 4G, Wifi, LAN (Optional) | |||
Communication Protocol | Modbus TCP/IP – Web server (Optional) | |||
Display Interface | 4.3-inch LCD or 7-inch centralized LED HMI panel | |||
Protecting | Over-voltage protection, Under-voltage protection, Inverter bridge inverse protection, Over-compensation protection | |||
CT alarm | Yes | |||
Event Recorded | On-site and remote monitoring capabilities. Reports data of power quality events up to 30 days. | |||
Monitoring | Support individual monitoring (4.3-inch touch screen) and centralized 7″ touch screen multilingual graphical HMI | |||
Mechanical Characteristics | ||||
Installation | Wall Mounted / Rack Mounted / Cabinet | |||
Rack Mount, LED (W*D*H, mm) | 500*515*180 | 500*546*190 | 500*605*269 | 500*722*370 |
Rack Mount, LCD (W*D*H, mm) | 500*515*180 | 500*586*190 | 500*630*269 | 500*722*370 |
Wall Mount, LCD (W*D*H, mm) | 500*180*540 | 500*190*571 | 500*273*638 | 500*370*722 |
Net Weight | 23 kg | 28 kg | 44 kg | 110 kg |
Color | Aluminium-Zinc alloy coated for rack mounted, LED type / RAL7035 for rack mount LCD and wall mounted type | |||
Environment Requirement | ||||
Altitude | Up to 1500 m | |||
Operation Temperature | – 10°C ~ 40°C | |||
Relative Humidity | 5 % – 95 %, non-condensing | |||
Protection Class | IP20, Other IP class customizable | |||
Qualifications | CE |
EX-Series
EX – Series – unmatched efficiency and technology
The world’s fastest, flexible and most energy effective multifunctional reactive power compensation system. The SVG have an excellent real time dynamic reactive power compensation capability. The EX series ultra-compact design and extreme low heat dissipation makes it suitable for space limited application and retrofit projects. The EX -series SVG are designed for integration into our standard cabinets or to be used as a wall mounted or integrated stand-alone PFC solution.
Key Features:
- Ultra high – 98,5% efficiency
- Extreme low heat dissipation
- Real-time dynamic VAR compensationy
- Load balancing
- Voltage control
- Ultra fast and accurate response
- Idle mode during low load (Standby)
- Non-over loadable
- Anti resonance protection and self diagnostic system
- Comprehensive monitoring system with high quality HMI
- Compact, modular and scalable design
Item | SVG | |
Rating | 50 kvar | 100 kvar |
Function | Reactive Power and Three Phase Unbalance Compensation | |
System Parameters | ||
Nominal Voltage | 380 V (-40 % ~ +20 %) (auto sensing). Connection to higher voltages through suitable step-up transformer. | |
Nominal Frequency | 50/60 Hz, auto sensing | |
Parallel modules | Unlimited scalability – Unlimited parallel capacity -Load shared evenly between modules | |
Efficiency | ≥ 98 % | |
Electrical system compatibility | 3-phase 3-wire and 3-phase 4-wire. | |
Performance Indicators | ||
Control Algorithm | FFT, Intelligent FFT and instantaneous reactive power | |
Reactive power compensation | Optimized, stepless and continuously adjustable power factor correction, leading (capacitive) and lagging (inductive). | |
Compensation Rate | > 99 % | |
Fast Response Time | < 50 μs | |
Full Response Time | < 15 ms | |
Target Power Factor | Adjustable from -1 to +1 | |
Switching Frequency | 20 kHz | |
Cooling Air Requirement | — | — |
Noise Level | < 56 dB | |
Communication Ports | RS485 and Ethernet Port (RJ45) / Option | |
Communication Protocols | Modbus RTU | |
Module Display Interface | 4.3-inch HMI (module) or 7″ centralized touch screen multilingual graphical HMI | |
Protection Functions | Over-voltage protection, Under-voltage protection, Inverter bridge inverse protection, Over-compensation protection | |
Mounting Type | Wall-mount modules, Rack-mounted modules and flexible Cabinet solutions | |
Dimensions (W*D*H, mm) | — | — |
Net Weight | — | — |
Storage Temperature | – 40º C ~ 70º C | |
Operating Ambient Temperature | – 10º C ~ 40º C | |
Relative Humidity | 5 % – 95 %, non-condensing | |
Protection Class | IP20 (other IP degrees on request) | |
Qualifications | CE | |
Standards Compliance |
H-Series
40H-series – Demanding applications and harsh environments
H-series Static VAR Generator are customized for demanding applications and are available from voltage level up to 690V in both 3W and 4W applications. Equipped with state-of-the-art monitoring and reporting functionality, the robust H-series SVG`s operate in harsh environments and are easily scalable. H-series SVG have UL-certificate of compliance.
Key Features:
- Real-time dynamic VAR compensation
- Load balancing
- Voltage control
- Voltage level up to 690V
- Ultra fast and accurate response
- Idle mode during low load (Standby)
- Non-over loadable
- Anti resonance protection and self diagnostic system
- Comprehensive monitoring system with high quality HMI
- Wall-mounted, rack mounted and flexible cabinet solutions
- Compact, modular and scalable design
Items | 480 V | 600 V | 690 V |
30/60/120/250 (KVAR) | 40/50/80/100 (KVAR) | 30/60/120 (KVAR) | |
System Parameter | |||
Input phase voltage range | 480 V (384 V – 552 V) | 600 V (420 V – 690 V) | 690 V (483 V – 793 V) |
Power grid frequency | 50/60 Hz (Auto frequency sensing) | ||
Parallel operation | Unlimited scalability – Unlimited parallel capacity -Load shared evenly between modules | ||
Efficiency | ≥ 97 % | ||
Power grid structure | 3P3W/3P4W | ||
CT Ratio | 150/5~30,000/5 | ||
Circuit topology | EMES 3-Level Topology | ||
Performance Indicator | |||
Rated capacity | Depending on voltage level – Modules available from 30 – 250 KVAR | ||
Functionality | Dynamic VAR compensation, Load Balancing, Voltage Control | ||
Control algorithm | Real time digital control, FFT/Intelligent FFT/Instantaneous reactive power | ||
Filtering range | 2nd to 50th order | ||
Harmonic Compensation Efficiency | > 97 % | ||
Reaction time | < 50 µs | ||
Overall response time | < 5 ms | ||
Target power factor | Adjustable from -1 to +1 | ||
Switching frequency | Average 20 kHz | ||
Cooling air requirement | For 25/35/50 A 725 CFM; For 60/75/100 A 761 CFM | ||
Noise level | < 65 dB | ||
Communication & Monitoring Capability | |||
Communication ports | RS485 and Ethernet TCP IP port(RJ45) – Optional remote access package (Web-server – 4G-WAN-WiFi-LAN) | ||
Communication protocols | MODBUS (RTU, TCP/IP) | ||
Module display interface | 7-inch LCD touch screen/LED (rack-mounted); 4.3-inch LCD touch screen (wall-mounted) | ||
Protection functions | Intelligent safety and protection system – Self diagnostic, anti-resonance system and Smart thermal management system | ||
Event history | Available | ||
Alarm history | Available | ||
Mechanical Properties | |||
Mounting type | Wall-mount/Rack-mount/Cabinet | ||
Dimensions (W*D*H) mm | For 25/35/50 A 500*540*180 (Rack-mounted) 500*184*627 (Wall-mounted) For 60/75/100 A 500*675*250 (Rack-mounted) 500*250*675 (Wall-mounted) | ||
Module net weight | 40 kg (25/35/50 A); 70 kg (60/75/100 A) | ||
Color | Aluminium-Zinc alloy coated | ||
Environment Requirement | |||
Altitude | ≤ 1500 m | ||
Ambient temperature | -20°C – 40°C | ||
Relative humidity | 5 % to 95 %, non-condensing | ||
Protection class | IP20 | ||
Related Qualifications & Standards | |||
Qualifications | CE, cULus | ||
Standards compliance |